TrussFormer: 3D printing large kinetic structures
Robert Kovacs, Alexandra Ion, Pedro Lopes, Tim Oesterreich, Johannes Filter, Philip Otto, Tobias Arndt, Nico Ring, Melvin Witte, Anton Synytsia, and Patrick Baudisch
In Proceedings of the 31th Annual ACM Symposium on User Interface Software and Technology (UIST ’18)
paper: PDF
ACM Digital Library
TrussFormer is an integrated end-to-end system that allows users to 3D print large-scale kinetic structures, i.e., structures that involve motion and deal with dynamic forces.
TrussFormer builds on TrussFab, from which it inherits the ability to create large-scale static truss structures from 3D printed hubs and PET bottles.
TrussFormer incorporates linear actuators into these rigid truss structures in a way that they move “organically”, i.e., hinge around multiple points at the same time. These structures are also known as variable geometry trusses. This is illustrated on the on the example of a static tetrahedron that is converted into a moving structure by swapping one edge with a linear actuator. The only required change is to introduce connectors that enable rotation, i.e. hinges.
![]()
Robert Kovacs, Alexandra Ion, Pedro Lopes, Tim Oesterreich, Johannes Filter, Philip Otto, Tobias Arndt, Nico Ring, Melvin Witte, Anton Synytsia, and Patrick Baudisch
In Proceedings of the 31th Annual ACM Symposium on User Interface Software and Technology (UIST ’18)
paper: PDF
ACM Digital Library
TrussFormer is an integrated end-to-end system that allows users to 3D print large-scale kinetic structures, i.e., structures that involve motion and deal with dynamic forces.
TrussFormer builds on TrussFab, from which it inherits the ability to create large-scale static truss structures from 3D printed hubs and PET bottles.
TrussFormer incorporates linear actuators into these rigid truss structures in a way that they move “organically”, i.e., hinge around multiple points at the same time. These structures are also known as variable geometry trusses. This is illustrated on the on the example of a static tetrahedron that is converted into a moving structure by swapping one edge with a linear actuator. The only required change is to introduce connectors that enable rotation, i.e. hinges.
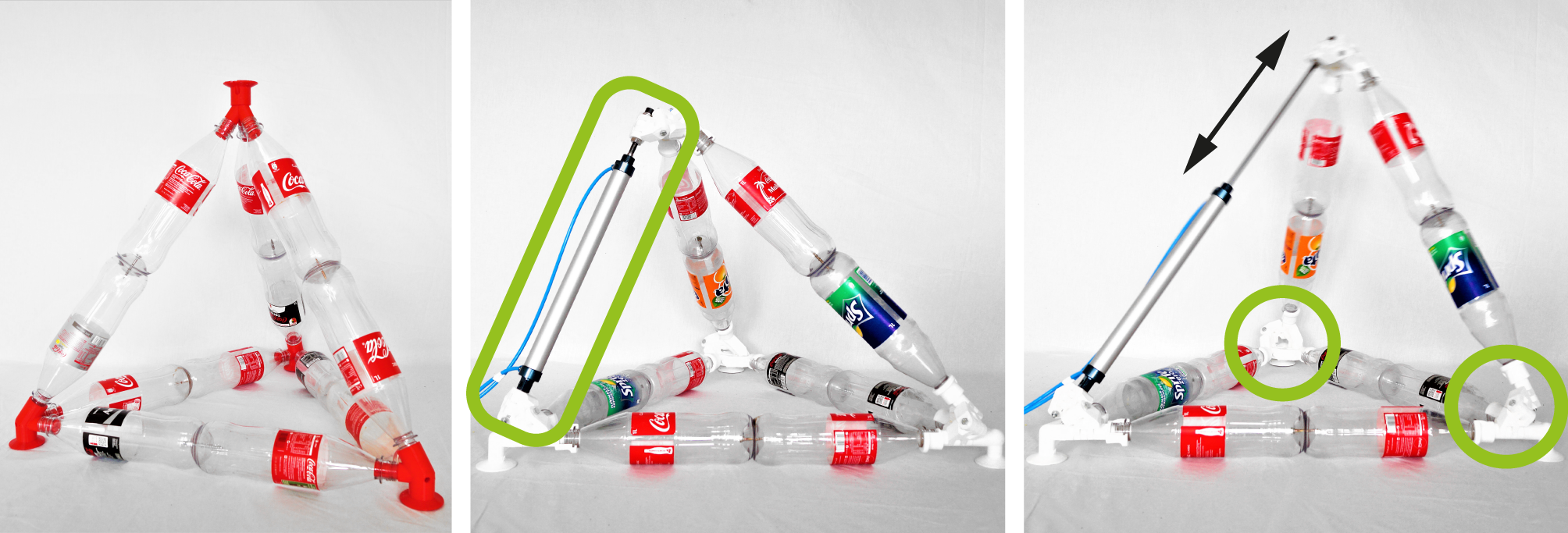
TrussFormer creates these mechanisms in six basic steps:
step 1: Creating the static structure. TrussFormer's editor’s ability to create static structures is based on TrussFab: users design the shape of their T-Rex using structurally stable primitives (tetrahedra and octahedra).
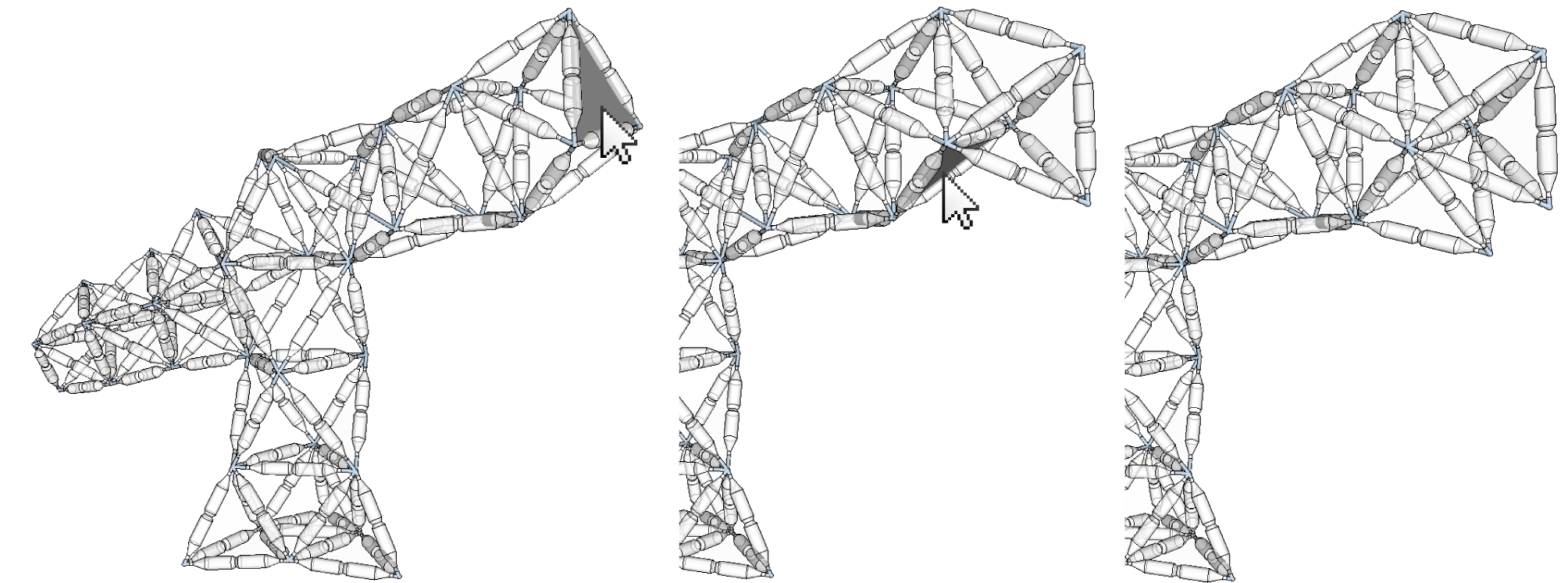
step 2: Adding movement. TrussFormer provides three different approaches to animate the structures, ranging from (1) automated placement (for novice users), through (2) placing elements with predefined motion, called assets, to (3) manual placement (as users acquire engineering knowledge). To add movement using the demonstrate movement tool, users pull the T-Rex head downwards. TrussFormer responds by placing an actuator that turns the T-Rex body into a structure that can bend down, as shown in the figure below.
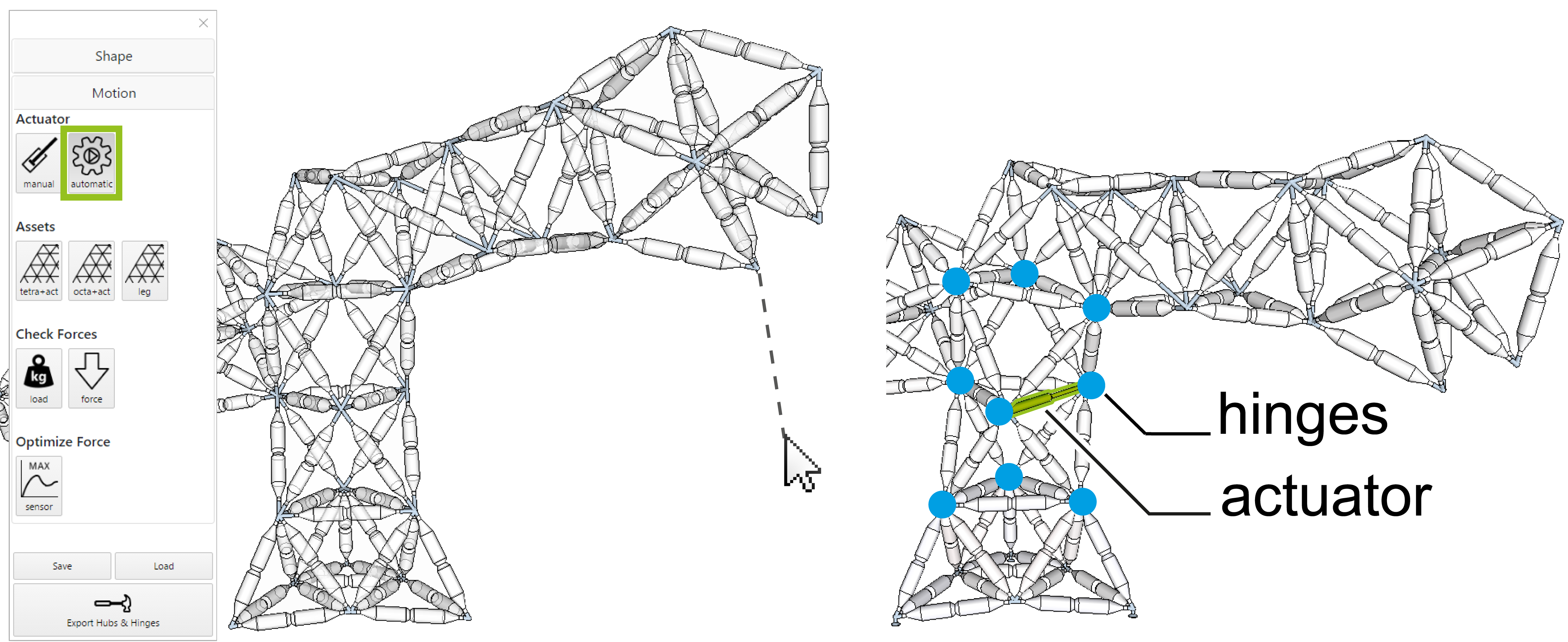
step 3: Stability check across poses. During this step, TrussFormer verifies that the mechanism is structurally sound. In the background, TrussFormer finds the safe range of expansion and contraction of the placed actuator by simulating the occurring forces in a range of positions. If there is a pose where the forces exceed the pre-determined breaking limits or the structure would tip over, TrussFormer sets the limits for the actuator so it will not extend beyond them. This check prevents users from producing invalid configurations.
step 4: Animation. To animate the structure users open the animation pane in the toolbar, as shown in the figure below. First, they control the movement of the structure manually using sliders, to try out the movement. When they find the desired pose, they simply add it as a keyframe to the animation timeline. With this TrussFormer allows users to orchestrate the movement of all actuators using a simple timeline/keyframe editor. Here, user programs a “feeding” behaviour, where the T-Rex opens its mouth while reaching down and waving its tail.
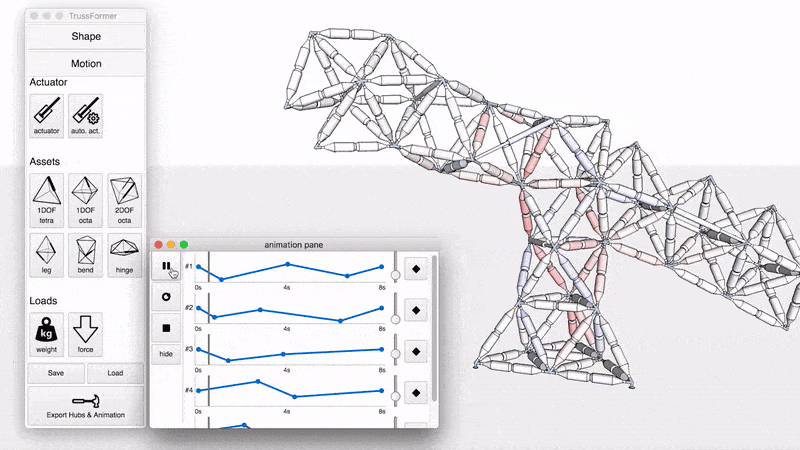
step 5: Checking the forces during the motion. Once the animation has been defined, TrussFormer computes the dynamic forces. In the figure below, (a) the user creates an animation that moves the T-Rex body up and down. (b) TrussFormer computes the forces while T-Rex’s body comes back up quickly after dipping down; the large acceleration of the long neck leads to very high inertial forces, exceeding the breaking limit of the construction, (c) causing the structure to fail at the indicated time point. These situations are hard to foresee, because the inertial forces can be multiple times higher than the static load in the structure. (d) TrussFormer addresses this by automatically correcting the animation sequence by either limiting the acceleration or the range of the movement, assuring that the structure will now withstand the movement.

step 6: Fabrication. When users are satisfied with their design (structure, movement and animation), they click the fabricate button. This invokes (1) TrussFormer’s hinge generation algorithm, which analyzes the structure’s motion and generates the appropriate 3D printable hinge and hub geometries, annotated with imprinted IDs for assembly. In the case of the T-Rex, the system exports 42 3D printed hubs, consisting of 135 unique hinging pieces.
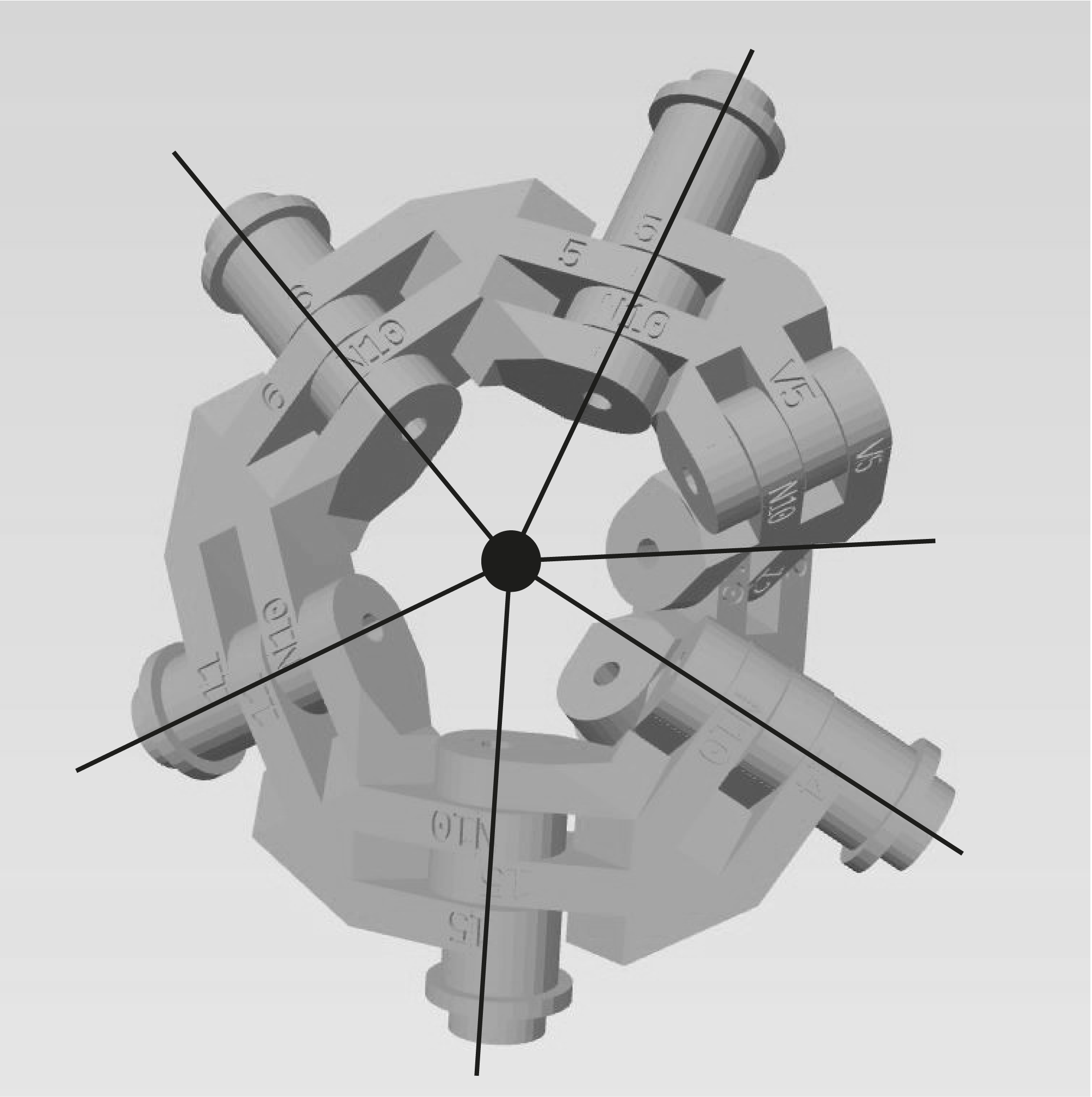
(2) Next, TrussFormer exports the created animation patterns as Arduino code that users upload to their microcontroller. (3) Lastly, it outputs a specification file, containing the force, speed, and motion range of the actuators, in order to achieve the desired animation pattern. Users find these actuators as standardized components.
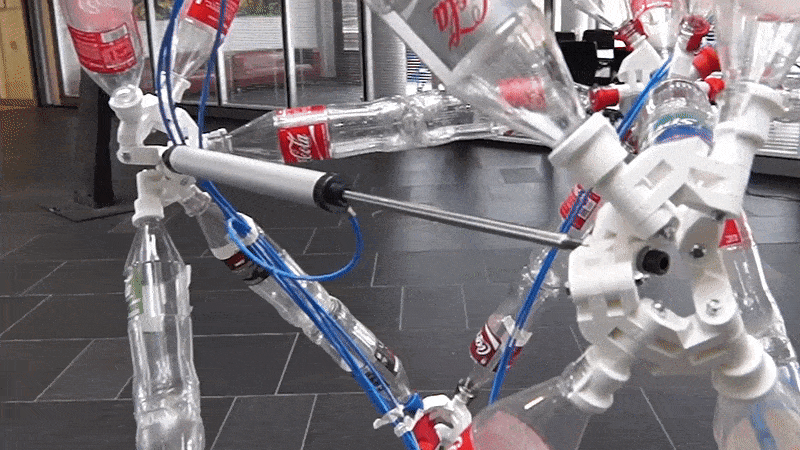
Conclusion
Our main contribution is this end-to-end system that enables non-expert users to create large-scale kinetic structures, such as the devices used in large-scale animatronics.
TrussFormer helps users in the 3 main steps along the design process. (1) It enables users to animate large truss structures by adding linear actuators to them. It offers three tools for this purpose: manual actuator placement, placement of assets performing predefined motion, and creating motion by demonstration. (2) TrussFormer validates the design in real time against static forces, static forces across all poses, and dynamic forces. (3) TrussFormer automatically generates the necessary 3D printable hinges for fabricating the structure. Its algorithm determines the placement and configuration of the hinges and their exact dimensions.
Talk at UIST2018
more:
official project page